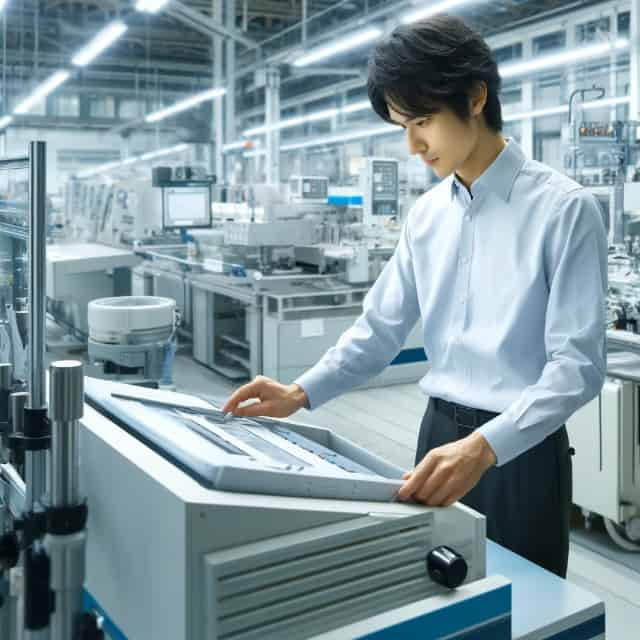
はじめに
リードタイムを短縮し生産効率を劇的に向上させることは、多くの企業が直面する重要な課題です。
この記事では、これらの目標を達成するための具体的な方法について詳しく掘り下げます。
最適化されたプロセスと効率的な資源配分によって、無駄を省き、生産ライン全体を改善するステップを示します。
特に、自動化技術やデジタルツールの活用が生産性向上にどのような効果をもたらすのかを明らかにし、読者が実際に行動に移せる実践的なアプローチを紹介します。
生産現場でのリードタイム短縮は、単なる時間削減以上のメリットをもたらします。
顧客満足度の向上、競争力の強化、コスト削減といった要素が密接に絡み合っています。
これらを実現するためには、どこから手をつけるべきか、どのように優先順位をつけるべきか、明確なビジョンが必要です。
この記事を通じて、具体的な手順と考慮すべき要素を理解し、実現可能な生産効率の向上に向けて一歩を踏み出しましょう。
作業工程を見直し、無駄を徹底的に排除したプロセス改善の実践方法
作業工程を効率化して無駄をなくす基本的なステップ
効率的な作業工程を構築するためには、まず現状のプロセスを細かく見直すことから始めます。
現場のどこで時間や資源が無駄になっているのかを特定し、それらを段階的に排除していきます。
具体例として、製品が次の工程に移るまでの待機時間を削減する取り組みが挙げられます。
無駄な作業をなくし、必要なタスクに集中することで、リードタイムの短縮が可能になります。
さらに、効率化のための手順を明確化し、誰でも同じ方法で作業できるように標準化することが重要です。
標準化されたプロセスにより、作業者の負担を軽減し、全体のスムーズな進行を支える基盤を築くことができるでしょう。
新しい作業工程を導入した後は、定期的にプロセスを見直し、さらなる改善点を見つけていくことも欠かせません。
また、作業工程を効率化する際には、全体的な生産計画やスケジュールを見直すことも検討すべきです。
作業者の配置やリソースの配分を最適化し、よりスムーズに生産が進む体制を整えることで、効率向上の効果を最大化できます。
これらの取り組みを通じて、作業工程の改善を実現し、生産性を向上させることが可能なのです。
動線を最適化し作業者の移動時間を大幅に削減する方法
作業者の動線を最適化することで、余分な移動を減らし、全体の生産スピードを向上させることができます。
作業スペース内での動線を分析し、無駄な歩行や搬送をなくすレイアウトの変更を行うことが効果的です。
例えば、頻繁に使うツールや材料を作業者の近くに配置することで、必要なものを探す時間を削減できるでしょう。
作業者の動線が合理化されると、移動に伴う疲労が軽減でき、作業効率が向上します。
作業者の動線が合理化されることによって、作業者一人ひとりが持つ本来の生産力を最大限に引き出すことが可能なのです。
動線の最適化は一度きりの改善で終わるものではなく、現場の状況に応じて柔軟に調整していくことが求められます。
さらに、動線を最適化する際には、設備の配置や作業エリアの広さも考慮する必要があります。
作業者がスムーズに移動できる十分なスペースを確保し、必要な設備が適切な場所に配置されているかどうかを確認することで、全体的な効率が向上します。
そして作業者が最短距離で必要なツールや材料にアクセスできる環境を整えることで、ストレスのない作業環境を実現できるでしょう。
各工程間の連携を強化しプロセスをスムーズにする具体的な方法
工程間の連携を強化するためには、情報共有とコミュニケーションの効率化が不可欠です。
作業進捗をリアルタイムで把握できるシステムを導入することで、次の工程を待つ時間を最小限に抑えることができます。
その結果、作業が滞ることなく、スムーズに進行します。
また、作業者同士や管理者との間で明確な目標と優先順位を共有することで、チーム全体の意識が統一できるでしょう。
例えば、日々のミーティングで進捗を確認し、問題が生じた際には迅速に対応するフローを確立することで、全体の効率が向上します。
工程間の連携を強化することで、リードタイム短縮と品質向上を同時に達成することが可能です。
さらに、工程間で使用されるツールや材料の標準化を進めることも有効です。
共通のフォーマットや基準を設けることで、情報のやり取りがスムーズになり、作業効率が高まるでしょう。
こうした取り組みは、各工程が独立していても全体として一貫性を保つのに役立ちます。
工程間の連携を強化し、全体的なプロセスの流れをスムーズにすることで、効率的な生産体制を構築できるのです。
ジャストインタイム導入で無駄のない在庫管理とリードタイム短縮を両立
適切な需要予測で無駄を徹底的に減らす方法
無駄をなくすためには、正確な需要予測が不可欠です。
過去のデータを活用して需要のトレンドを分析し、製品を必要な量だけ生産する計画を立てることで、余剰在庫を減らすことができます。
余剰在庫を減らすことができることで、保管コストの削減と資金効率の向上が実現します。
需要予測を適切に行うことで、無駄な材料購入や過剰な生産を防ぎ、スムーズな生産体制を整えることが可能です。
その結果、リードタイムの短縮とコスト削減が一石二鳥で実現します。
さらに、需要予測を行う際には、最新のデータ分析ツールやAI技術を活用することで、精度を高めることができるでしょう。
需要予測の精度を高めることで、市場の変化や季節的な需要の変動に迅速に対応できるようになり、在庫を最適なレベルで維持することが可能です。
こうした予測技術を活用することで、無駄を排除し効率的な生産体制を実現できるのです。
生産計画の精度を最大限に高めるための具体的手法
生産計画を正確に立てるためには、需要予測に基づいてスケジュールを組み、各工程のリソース配分を最適化することが重要です。
生産ラインの稼働状況や納期に合わせて計画を調整することで、効率的な生産が可能になります。
例えば、生産スケジュールを短期間で見直し、現場の状況に応じて柔軟に変更できる体制を整えると、予期しないトラブルにも迅速に対応できます。
効率的な生産が可能になることによって、製品の生産から出荷までの流れをスムーズに保つことができます。
また、生産計画を精度良く進めるためには、作業者や管理者との定期的なコミュニケーションも重要です。
計画の進捗を共有し、現場からのフィードバックを取り入れることで、より現実的で効果的な生産スケジュールを策定できるでしょう。
その結果、リードタイム短縮を達成するための確実な基盤を築くことが可能なのです。
バックアップサプライヤーを活用して供給リスクを最小限に抑える方法
サプライチェーンのリスクを減らすためには、複数の供給業者を確保しておくことが重要です。
メインサプライヤーに問題が発生した場合でも、バックアップの業者を活用することで迅速に対応できます。
その結果、生産が止まるリスクを回避し、安定した供給を維持できるでしょう。
複数の供給元を持つことで、特定のサプライヤーに過度に依存するリスクを軽減し、全体的な生産の信頼性を向上させることができます。
サプライチェーンを堅固に保つことは、リードタイム短縮においても重要な要素です。
また、バックアップサプライヤーを選定する際には、コストだけでなく品質や納期の信頼性も考慮する必要があります。
信頼できる供給業者と継続的に良好な関係を築くことで、安定した生産体制を保つことが可能です。
このようにして供給リスクを低減し、スムーズな生産を維持できるのです。
デジタル化と多能工化を活用して生産フローを根本的に改善
生産性をリアルタイムで可視化する先進的デジタル技術の活用法
デジタル技術を活用することで、生産工程全体の可視性を高めることができます。
たとえば、IoTセンサーやデータ分析ツールを導入することで、各工程の進捗や機器の稼働状況をリアルタイムで把握できます。
この情報に基づいて迅速な意思決定が可能になり、生産ラインのボトルネックを素早く特定して改善できるでしょう。
また、デジタル化による生産性の向上は、トラブルが発生した際にも迅速な対応を可能にします。
異常が検出された場合には、即座に原因を特定し適切な処置を行うことで、全体の効率を維持することが可能です。
全体の効率が維持できることによって、生産現場における問題解決能力が向上し、安定した生産体制を築くことができます。
さらに、デジタル技術を活用することで、リソースの最適化や品質管理の向上も実現します。
生産工程の各段階で得られるデータをもとに、より正確な判断ができるため、無駄を排除し効率的な生産を推進できるでしょう。
こうしたデジタル化の取り組みを進めることで、企業全体の生産性が向上します。
多能工化を推進して柔軟なスタッフ配置を実現する手法
多能工化を進めることで、作業者が複数の工程に対応できるようになります。
多能工化を進めることによって、特定の工程に作業者が集中しすぎる状況を回避し、全体的な人員配置を最適化することが可能です。
例えば、ある工程で急な需要増加があった場合でも、別の工程からスキルを持つスタッフを迅速に移動させることができます。
柔軟なスタッフ配置によって、リソースの無駄を減らし、全体の効率を高めることができます。
また、作業者が複数のスキルを持つことで、個々の成長機会も広がり、働きがいの向上にもつながるでしょう。
多能工化は、効率的な生産ラインの構築において欠かせない要素です。
さらに、多能工化を進めるためには、従業員への継続的なトレーニングとスキル向上の支援が重要です。
作業者が新しいスキルを習得しやすい環境を提供することで、スタッフ全体の能力が向上し、柔軟で効率的な生産体制を築くことが可能になります。
その結果、企業全体の生産性が向上し、競争力が強化できるのです。
ボトルネックを解消し生産ライン全体を最適化する方法
生産ラインのボトルネックを特定し解消することは、生産フローを改善するための重要なステップです。
ボトルネックが発生する原因を分析し、適切な対策を講じることで、生産全体の流れをスムーズに保つことができます。
例えば、特定の工程で頻繁に発生する遅延を改善するために、自動化設備を導入したり、作業手順を見直したりすることで、流れを円滑にすることができるでしょう。
ボトルネックの発生原因を分析することによって、リードタイムの短縮と生産性の向上を同時に実現できます。
生産ラインの最適化は、継続的な改善プロセスを通じて達成できるでしょう。
現場のフィードバックを取り入れながら、絶えず改善を重ねることで、効率的な生産体制を維持することが可能です。
また、ボトルネックの解消に向けて、現場スタッフとの連携を強化し、迅速に対応できる体制を整えることも重要です。
その結果、安定した生産ラインを維持し、競争力を高めることができるのです。
まとめ
リードタイム短縮と生産効率向上を実現するためには、プロセスの最適化、自動化技術の導入、スタッフの柔軟な配置とスキル向上など、さまざまな取り組みが必要です。
これらの方法を組み合わせて実行することで、無駄を徹底的に排除し、生産ライン全体の効率を高めることができるでしょう。
また、需要予測の精度を高めることで、過剰な在庫や生産過剰を防ぎ、適切な資源配分を可能にします。
デジタル化と多能工化を活用することで、生産現場の柔軟性を向上させ、リスク管理能力を強化することも重要です。
これらの取り組みによって、顧客満足度の向上とコスト削減を同時に実現し、競争力を高めることができるのです。
生産現場でのリードタイム短縮は、効率的な生産体制の構築に直結します。
具体的な方法を理解し、計画的に実行することで、持続可能な成果を得ることが可能です。
そして、企業としての成長と成功に向けて、これらの戦略を取り入れ、実践していくことが求められるでしょう。